MSU students, faculty, staff and visitors produced over 5.4 million pounds of recyclable materials and 1.4 million pounds of organic waste in 2022. But where did it all go after we threw it in the recycling bin?
MSU Recycling Operations Coordinator Christopher Hewitt gave The State News a tour of the MSU Recycling facility. We broke down the processes that typical recyclables and food waste undergo, step-by-step.
Recyclable materials
Step one: Labeled bins on campus collect recyclables. In most campus buildings, recycling is organized into plastic and metal, mixed paper, cardboard and office paper. Hewitt said this step improves efficiency. About 96% of the items sent to MSU Recycling are recycled, considerably higher than most U.S. recycling plants.
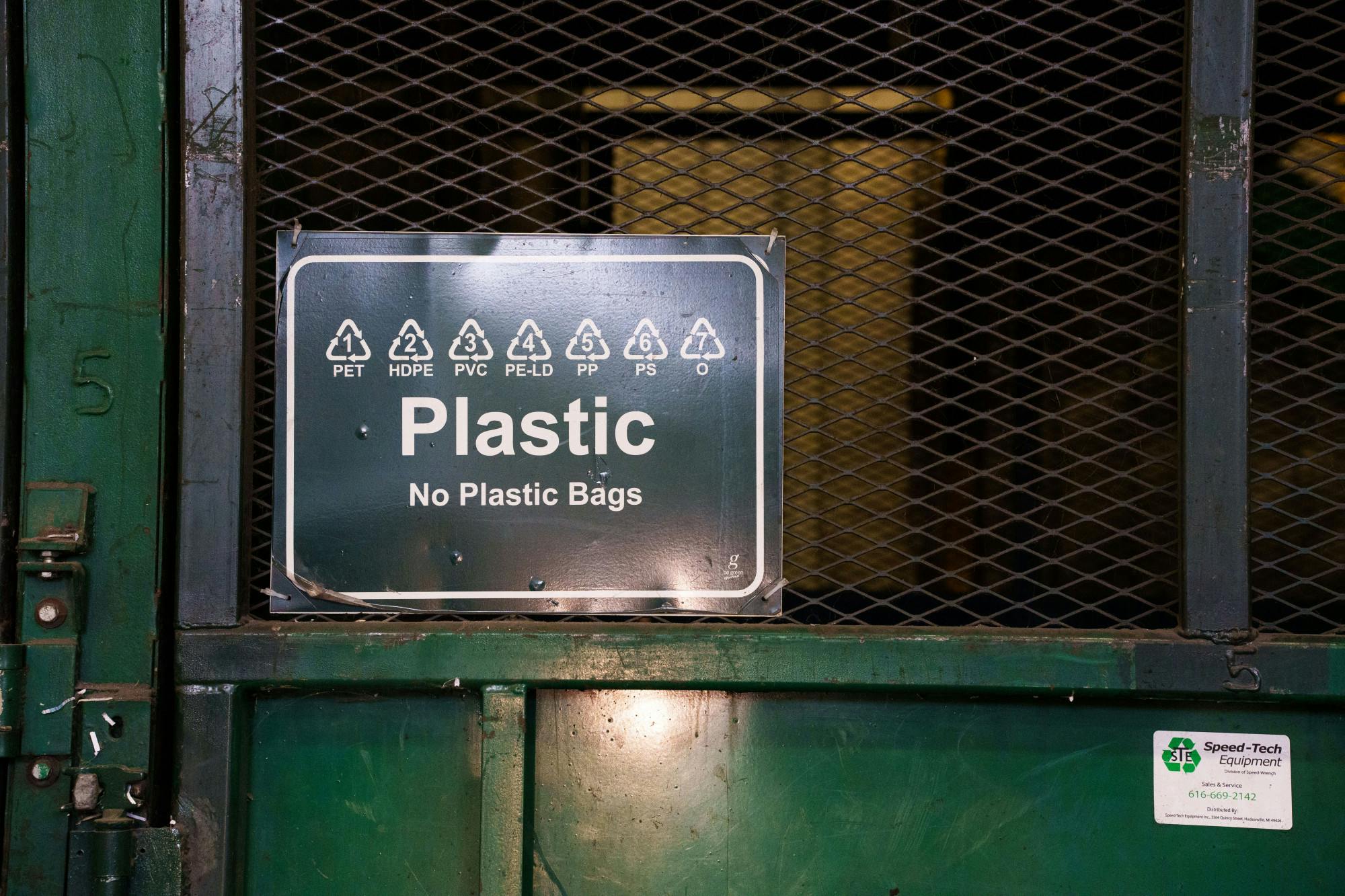
Step two: Trucks pick up items outside of buildings nearly every day. This process was made more efficient during the COVID-19 pandemic, as MSU Recycling developed an app to track when items should be picked up. Custodians use the app to alert MSU Recycling when bins are getting full. This has reduced the number of trips by 1,000 per month.
Hewitt said this innovation saves fuel and road space since the large trucks get two miles per gallon. The trucks take the recyclables to the Material Recovery Facility, or MRF, and dump them there.
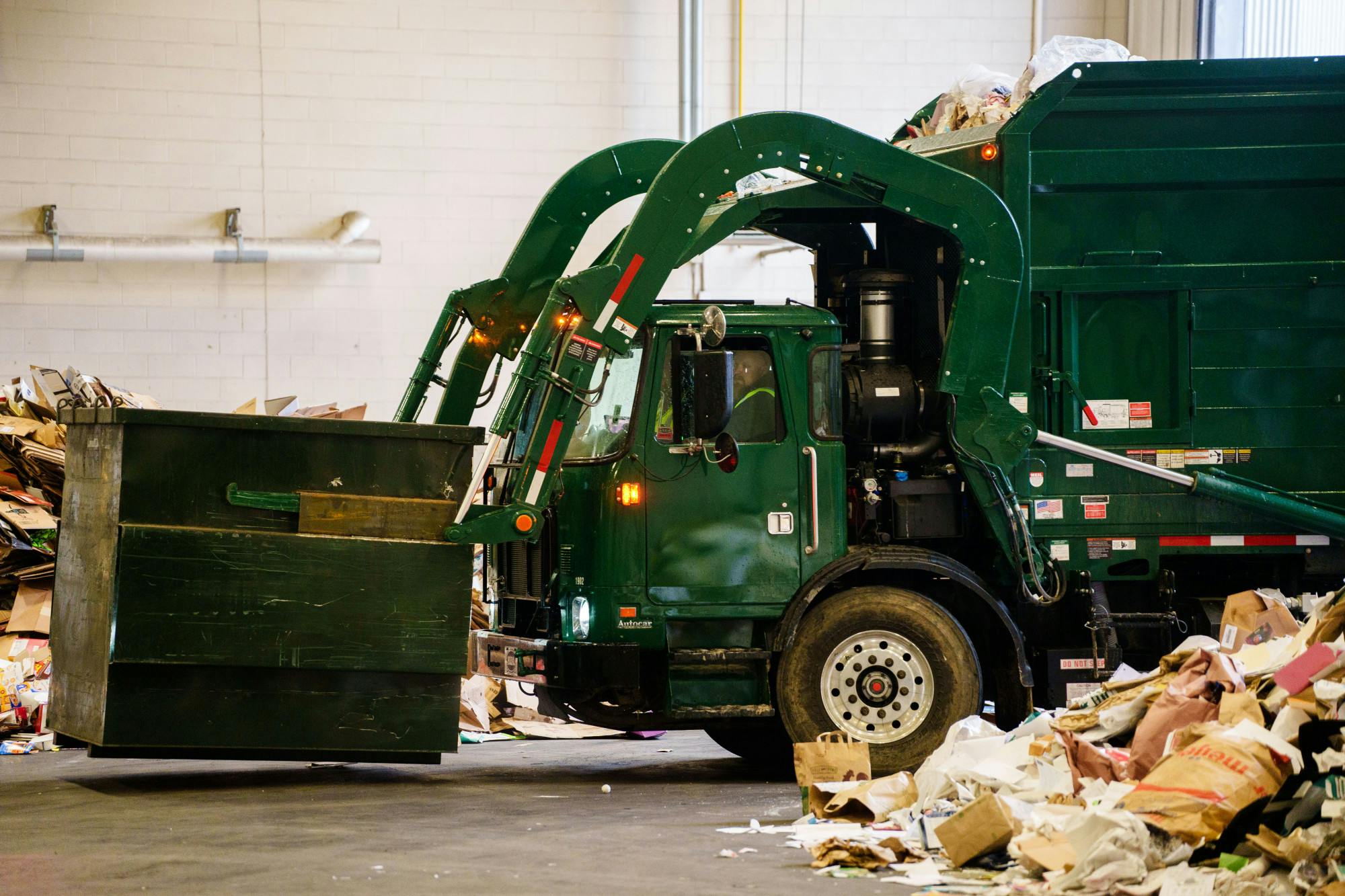
Step three: Items are sorted by hand. MSU Recycling workers place the sorted items from the trucks into large piles based on material. Workers then use loaders to place items from each pile onto a conveyor belt.
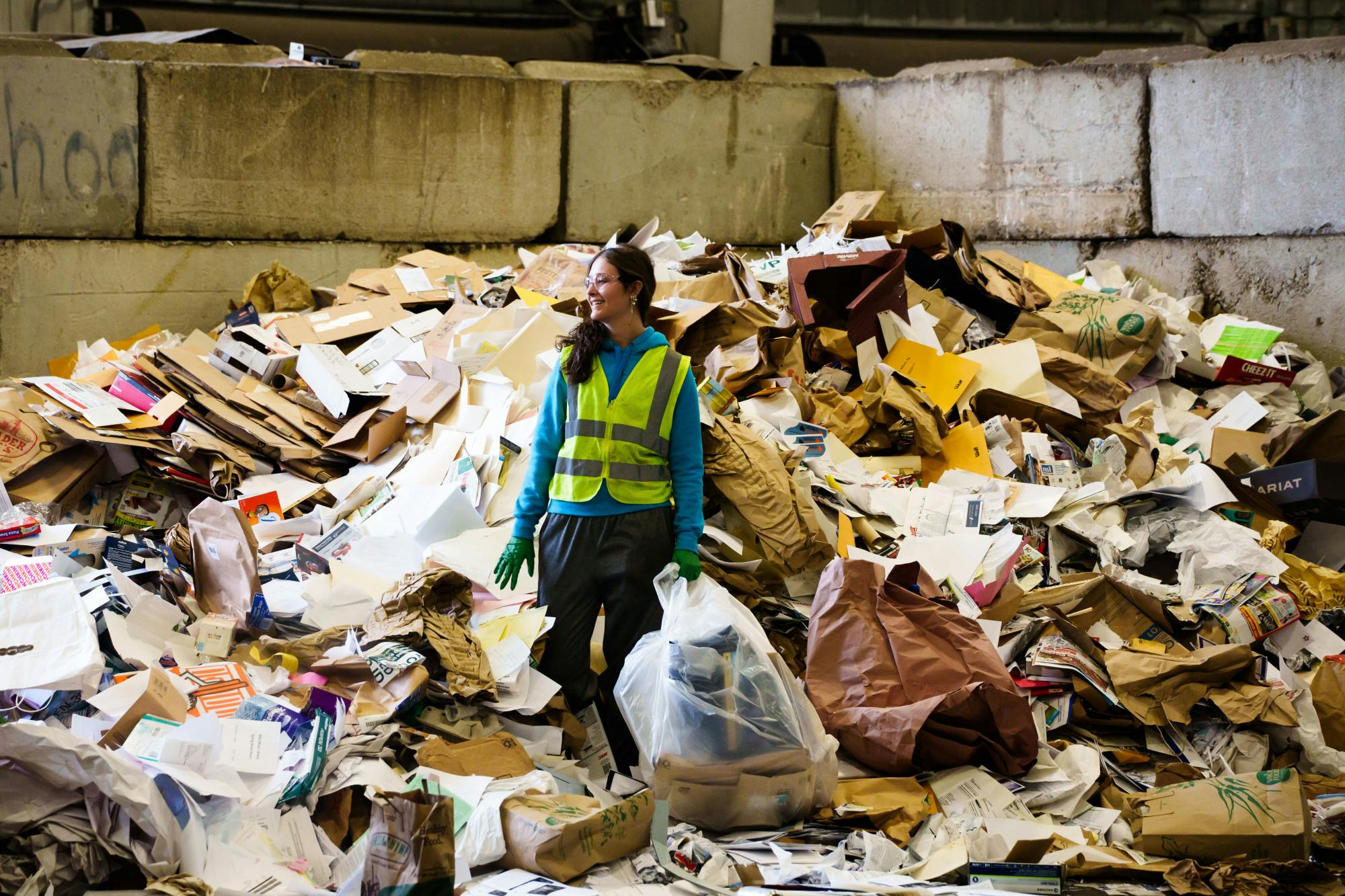
Step four: Workers and a robot further sort the items. The items go up the conveyor belt to a group of workers and a robot who separate the items based on type and drop them into labeled storage cages.
At the end of the conveyor, items that are non-recyclables or too dirty to be recycled are dumped in the trash. MSU Recycling got the robot a year ago and it has improved the process significantly, Hewitt said. Not only does it sort 80 items per minute, but it also allows the job to be safer for workers since they do not have to touch broken glass or unsanitary items. Up to 14,000 objects are sorted per day.
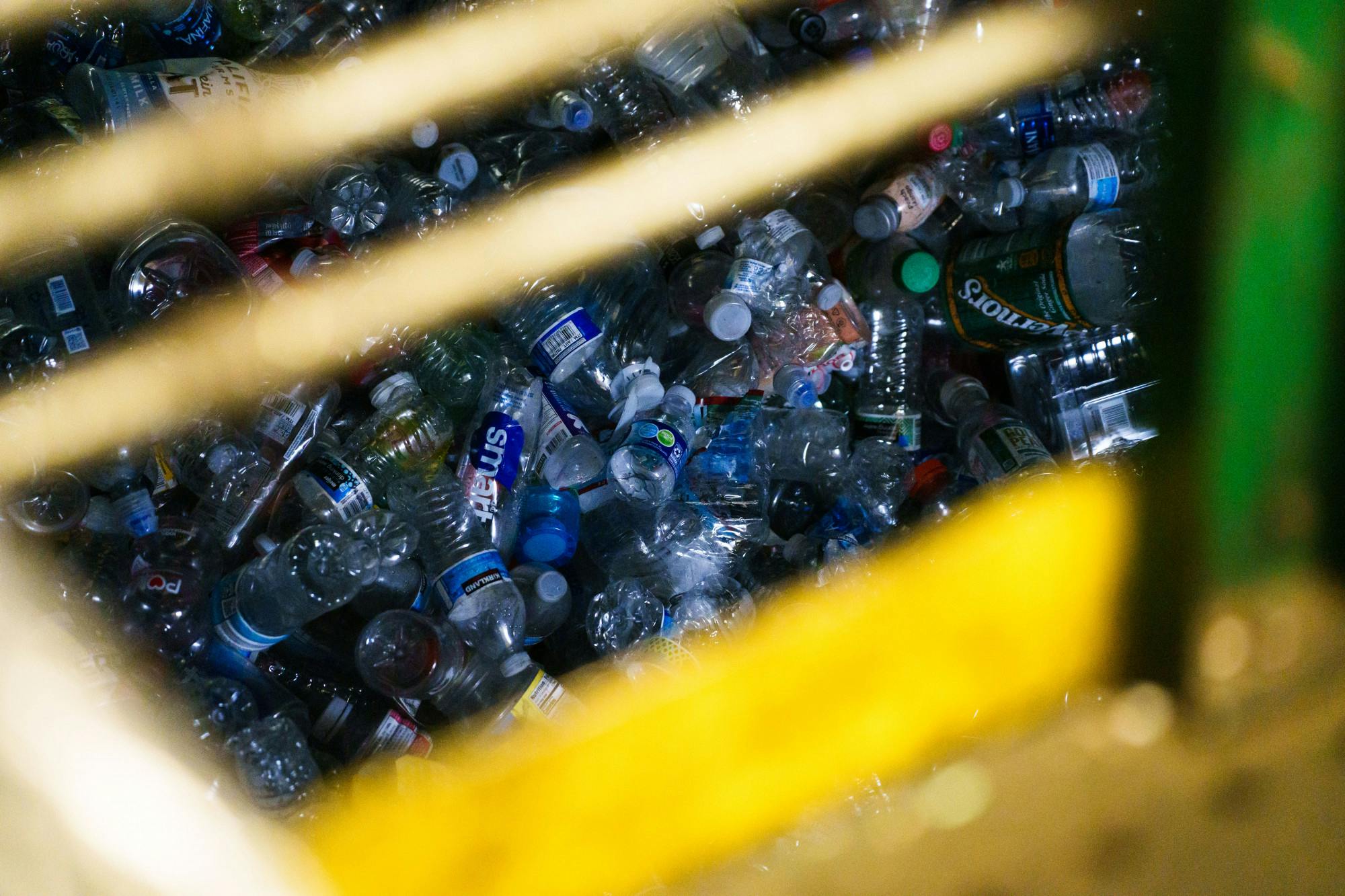
Step five: A machine compresses the recycled materials into bales. Once each cage is full, its contents are emptied onto a conveyor belt and taken to the baler. Workers then operate the machines to create each bale. They make between 12 to 15 bales per day and leave them to sit for a few weeks so remaining liquid can dry. Cardboard bales tend to be approximately 1,500 pounds.
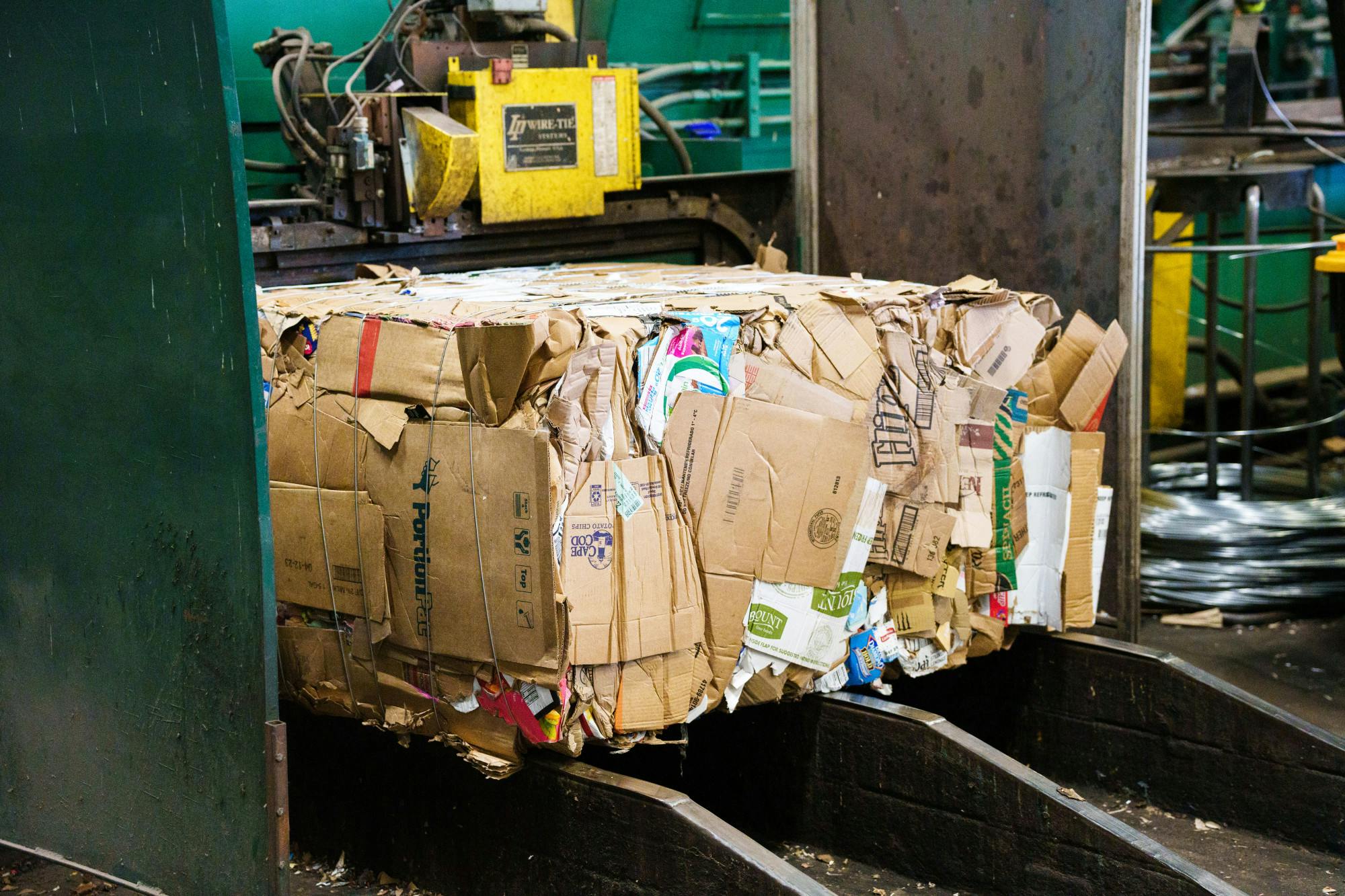
Step six: MSU Recycling sells the bales to manufacturers to be turned into new items. Bales vary in price based on material. For example, cardboard, which makes up about two-thirds of MSU’s recycled materials, costs about $75 per ton. However, the price of plastic fluctuates constantly since oil is an ingredient in plastic.
Hewitt said the price of a ton of plastic reached up to $2,000 during the COVID-19 pandemic. To sell for the best prices, MSU Recycling uses a broker who finds the most profitable deal.
Since MSU Recycling is mostly self-funded, the profit, along with profit from the MSU Surplus Store, is used to sustain the operation. Last year, they made about $375,000. Ninety-five percent of the recycling was sent to manufacturers in Michigan, which Hewitt said helps support Michigan businesses and lowers emissions and transportation costs.
Food waste
Step one: Trucks collect food waste. Leftover food from the dining halls is taken to MRF to prepare for composting.
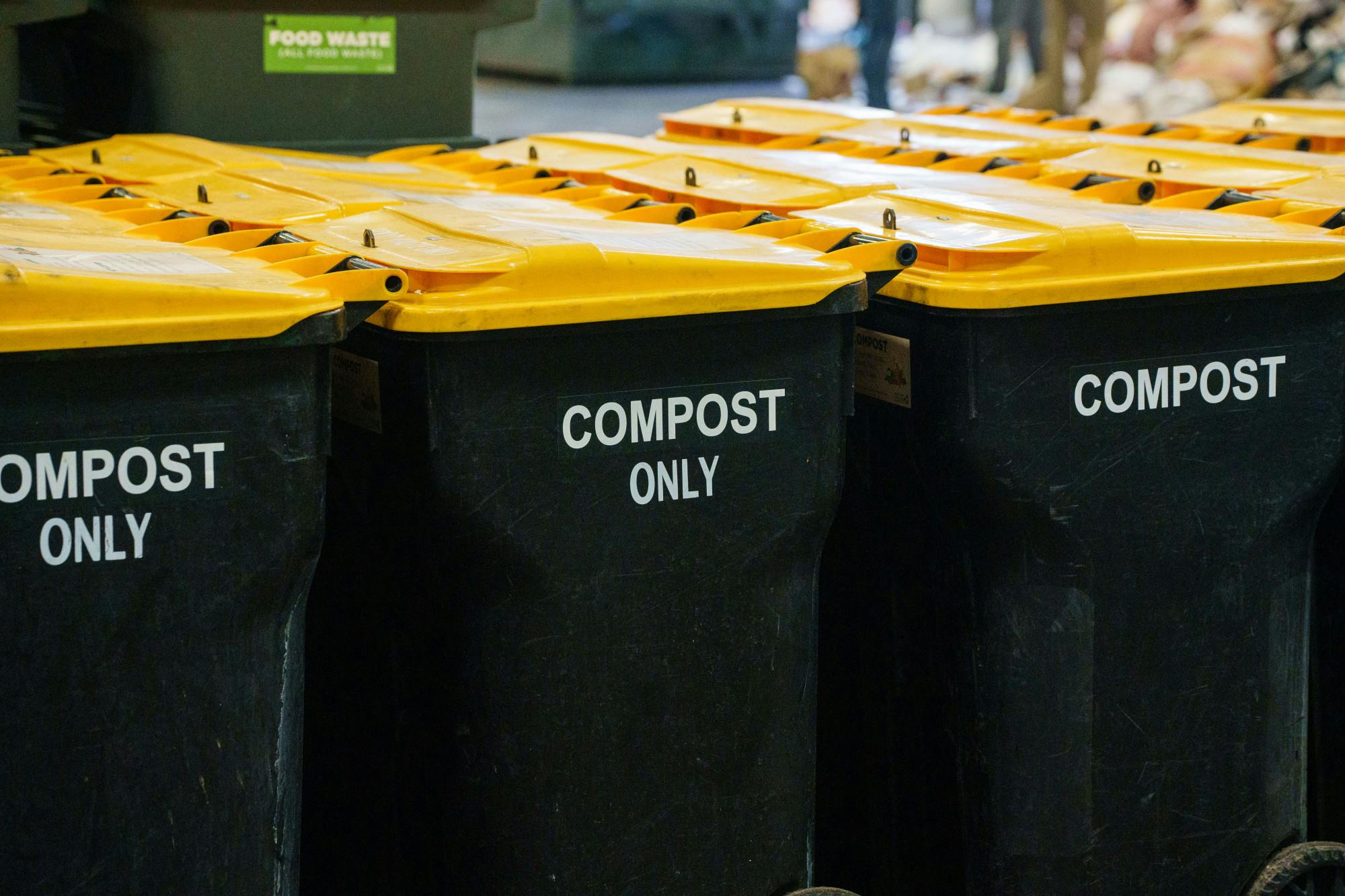
Step two: Workers split the waste into two categories: 40% vegan, unprocessed foods and 60% meat, processed foods. Hewitt said this step is crucial in protecting the composting worms from the crystals that form in processed foods during decomposition. The processed food is shipped to Hammond Farms to be hot composted and the unprocessed food is hot composted on site to kill pathogens that may harm the worms.
Step three: The remaining food waste is mixed with shredded paper and placed in a greenhouse to continue composting. The shredded paper is recycled from campus, though Hewitt said none of it is from confidential documents. This step lasts several months until the food has completely decomposed.
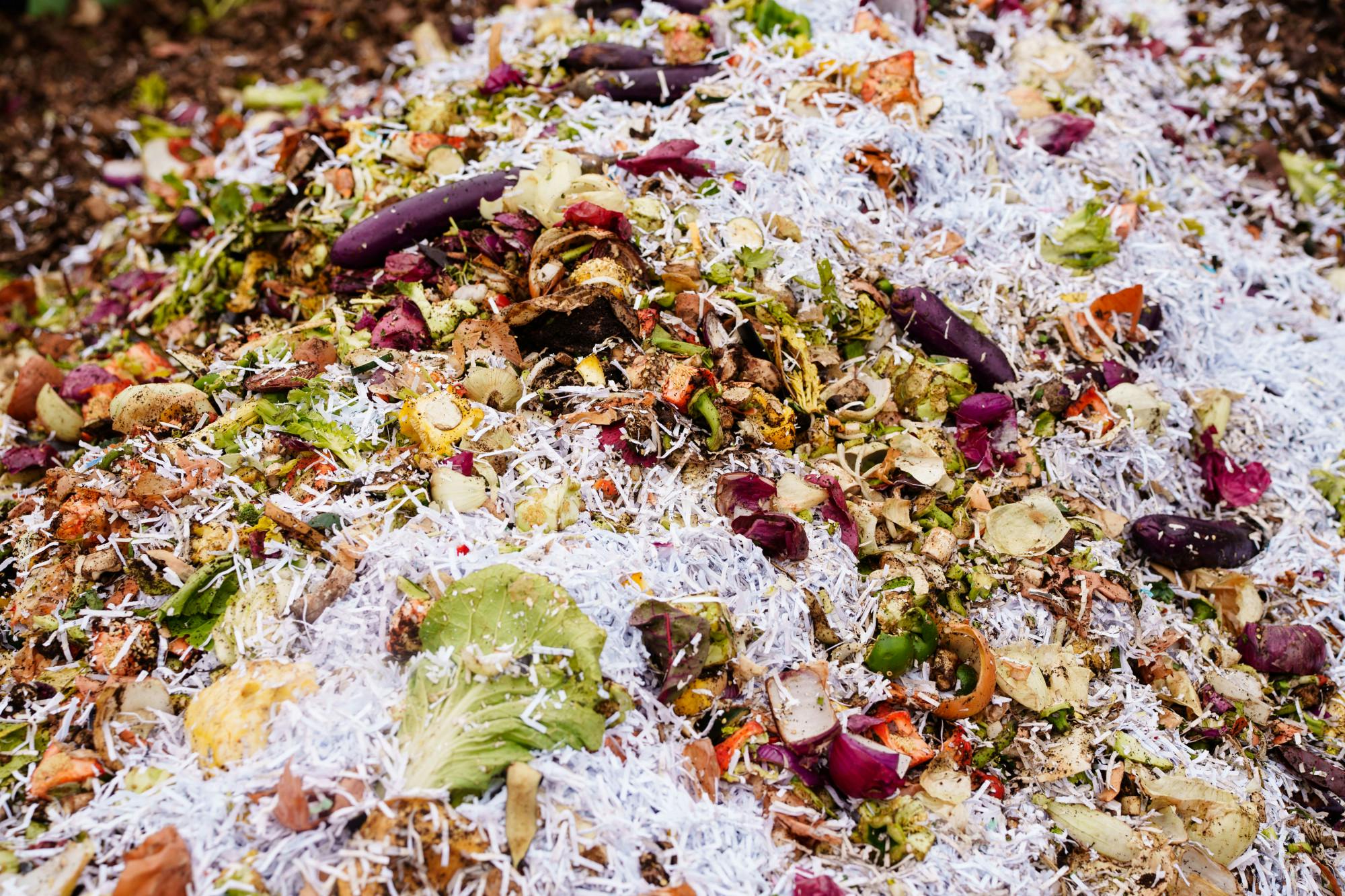
Step four: The decomposed material is fed to worms. The waste is transferred to another greenhouse with red wigglers and pot worms. These worms spend all of their time eating and reproducing. In fact, the original worm count was in the thousands and it is now estimated to be about 2 million.
The worms then excrete the food, creating a product called "vermicompost" that can be used as a fertilizer.
Hewitt said this step can be difficult because worms are most active in the summer, when MSU produces the least amount of waste. However, if it’s sunny, the greenhouse can get up to 70 degrees Fahrenheit in the winter — so the worms are more active.
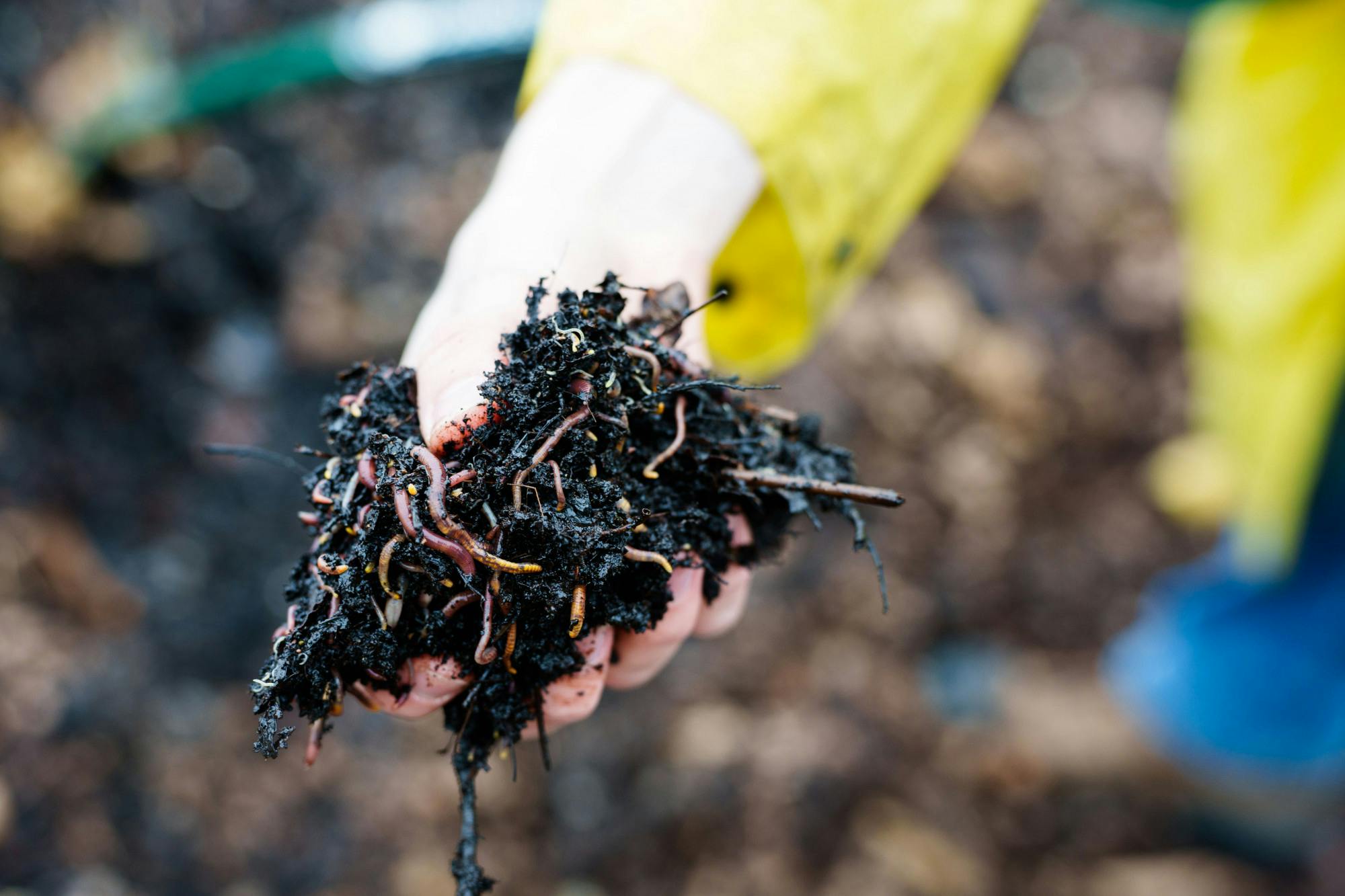
Step five: Workers collect and sell the vermicompost. Because the worms travel toward moisture, once they are done eating a section of vermicompost it can be collected and packaged. Some of the vermicompost is used on campus in gardens and the rest is sold to the public for less than half the market price. Altogether, the process takes about six months per batch.